Achieving Welding Excellence: Revealing the Tricks of WPS Application and Optimization
In the world of welding, achieving excellence is a pursuit that pivots on the meticulous execution and optimization of Welding Treatment Requirements (WPS) These fundamental papers work as the backbone of welding operations, determining the procedures and specifications required for creating top quality welds continually. However, the keys to unlocking the full capacity of WPS exist not just in recognizing its value but additionally in understanding the details of its implementation and optimization. By diving right into the key aspects, strategies, difficulties, and ideal methods related to WPS, a globe of welding quality waits for those who are prepared to discover its depths.
Significance of WPS in Welding
The Relevance of Welding Procedure Requirements (WPS) in the welding sector can not be overemphasized, working as the foundation for making sure uniformity, top quality, and security in welding operations. A WPS offers comprehensive directions on exactly how welding is to be executed, including vital variables such as products, welding processes, joint style, filler steels, preheat and interpass temperature levels, welding currents, voltages, traveling speeds, and much more. By adhering to a well-defined WPS, welders can maintain harmony in their job, resulting in constant weld quality throughout different jobs.
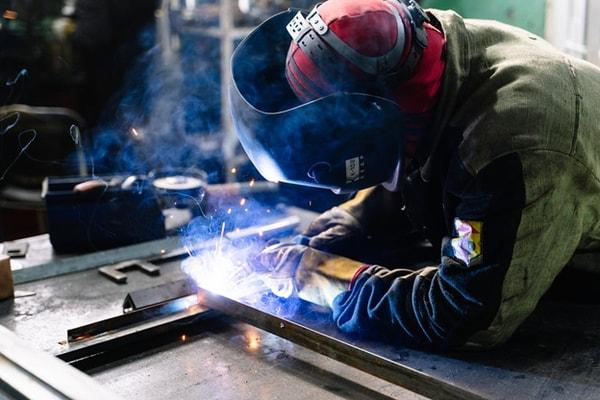
Crucial Element of WPS
Going over the integral elements of a welding treatment specification (WPS) is crucial for understanding its duty in welding operations. An extensive WPS consists of several crucial elements that lead welders in accomplishing top quality and consistency in their work. One vital aspect of a WPS is the welding process spec, which details the particular welding processes to be utilized, such as gas tungsten arc welding (GTAW) or secured steel arc welding (SMAW) Furthermore, the WPS includes details on the welding products, such as the kind and specifications of the base metal and filler metal to be utilized. The WPS additionally specifies essential variables like welding criteria, preheat and interpass temperature demands, and post-weld warm therapy procedures. In addition, it consists of information on joint design, fit-up, and any type of special methods or preventative measures essential for the welding procedure. By including these key elements into the WPS, welding procedures can be standardized, making certain high quality, effectiveness, and safety in welding procedures.
Strategies for WPS Optimization

Secondly, training and credentials of welding workers according to the details needs of the WPS is extremely important. Supplying comprehensive training programs and making sure that welders are licensed to execute procedures detailed in the WPS can bring about greater top quality welds and decreased rework.
Additionally, leveraging technology such as welding software application and monitoring systems can assist in enhancing WPS. These devices can assist in monitoring variables, ensuring parameters are within look at this site defined limitations, and giving real-time comments to welders, allowing them to make prompt changes for improved weld quality.
Typical Obstacles and Solutions
Dealing with barriers in executing the techniques for WPS optimization can prevent welding operations' efficiency and quality. One typical challenge is inadequate training or understanding of the welding treatment specs (WPS) among the welding team.
One more difficulty is the lack of proper paperwork and record-keeping, which is crucial for WPS optimization. Without clear documents of welding parameters, materials made use of, and evaluation results, it comes to be challenging to determine locations for improvement and ensure consistency in welding procedures. Carrying out a robust documents system, such as digital welding monitoring software application, can aid simplify record-keeping and facilitate data evaluation for continual renovation.
Additionally, inconsistent welding equipment calibration and upkeep can posture a substantial difficulty to WPS optimization. Regular tools checks, calibration, and upkeep schedules need to be complied with purely to make certain that welding parameters are accurately managed and kept within the defined resistances (welding WPS). By addressing these common obstacles with aggressive services, welding procedures can improve effectiveness, quality, and total welding quality
Finest Practices for WPS Application
To ensure successful WPS application in welding operations, adherence to sector requirements and precise attention to information are paramount. When starting WPS application, it is critical to begin by completely recognizing the particular welding demands of the project. This entails a comprehensive review of the welding procedure specifications, materials to be welded, and the environmental problems in which the welding will certainly occur.
As soon as the needs are clear, the following step is to pick the appropriate welding procedure that lines up with these requirements. This includes speaking with the pertinent codes and standards, such as those supplied by the American Welding Society (AWS) or the International Company for Standardization (ISO), to guarantee conformity and quality.
In addition, recording the whole WPS execution procedure is crucial for traceability and quality assurance. Comprehensive records ought to be kept regarding welding specifications, material prep work, preheat and interpass temperature levels, welding consumables used, and any discrepancies from the initial procedure. Normal audits and testimonials of the WPS can assist recognize locations for renovation and ensure recurring optimization of the welding procedure.
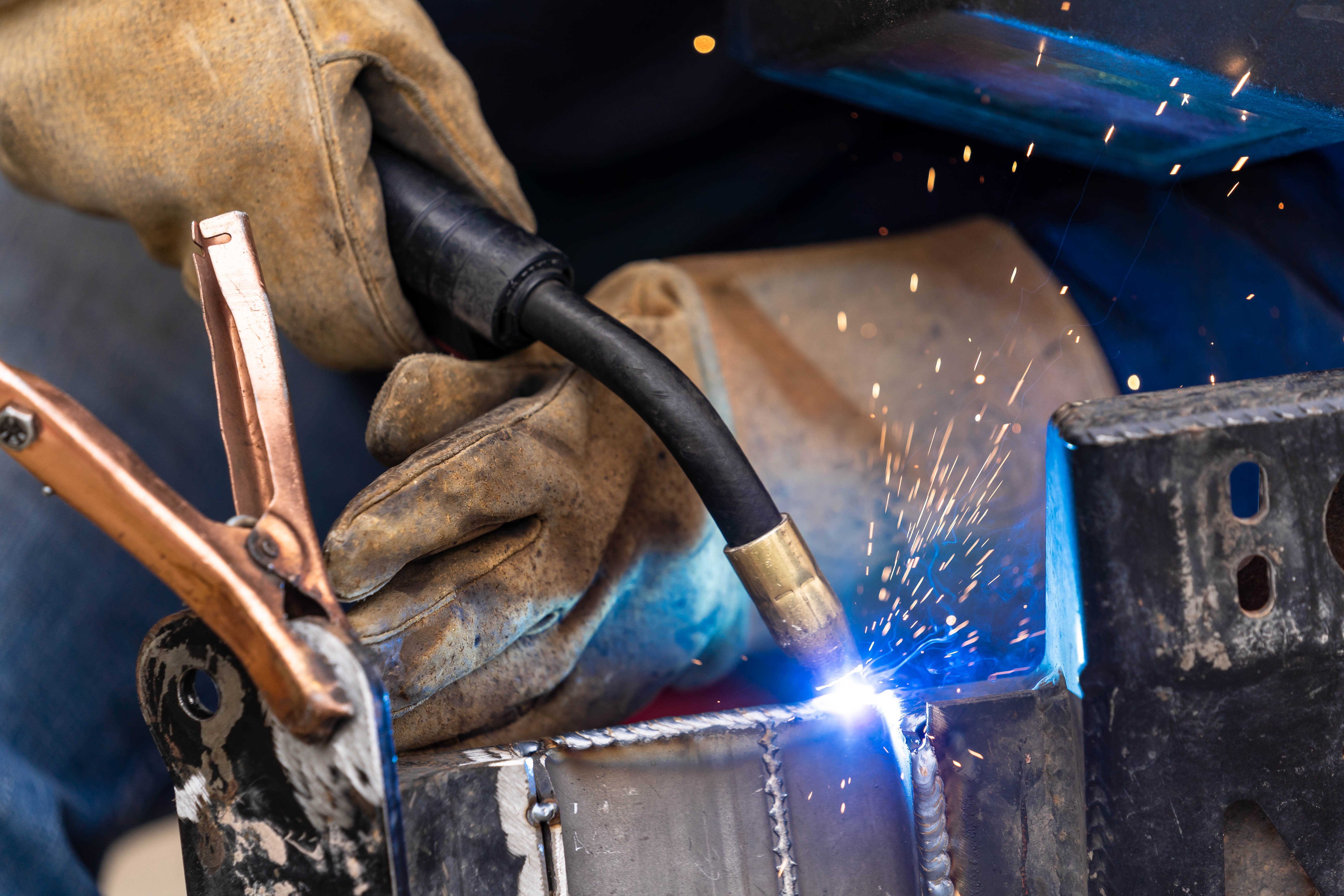
Final Thought
Finally, the implementation and optimization of Welding Procedure Specifications (WPS) is critical for more attaining welding quality. By understanding the crucial elements of WPS, applying effective approaches for optimization, dealing with common difficulties, and complying with finest practices, welders can guarantee top quality welds and risk-free working conditions. It is crucial for specialists in the welding sector to prioritize the correct application of WPS to improve overall welding efficiency and achieve wanted outcomes.
The Importance of Welding Procedure Requirements (WPS) in the welding industry can not be overstated, offering as the backbone for making certain consistency, top quality, and safety and security in welding procedures. A WPS offers detailed guidelines on how welding is to be brought out, consisting news of essential variables such as materials, welding processes, joint design, filler metals, interpass and preheat temperatures, welding currents, voltages, travel rates, and a lot more. One crucial element of a WPS is the welding process specification, which details the specific welding processes to be utilized, such as gas tungsten arc welding (GTAW) or protected metal arc welding (SMAW) By integrating these vital aspects right into the WPS, welding treatments can be standard, making certain quality, efficiency, and security in welding operations.
It is important for professionals in the welding industry to prioritize the proper execution of WPS to improve general welding performance and attain desired end results.
Comments on “Why a Welding WPS is Crucial: Enhancing Uniformity and Conformity”